Tire building machinery system is the core production process equipment designed to make tires, which has significantly transformed the tire industry.Fetiresatures of automatic pre-building machinery are high degree of automation (including auto-switch), easy operation (i.e. no need after a person who can operate it properly), and huge production capacity (as many as several hundred sets per day). These may be important also for understanding just how much variety there is among manufacturers and the extent to which their individual plants have been influenced by external factors-Tire building machinery refers to the complex systems and equipment used to assemble various components of a tire, such as rubber, fabric and steel belts, into a finished product for sale on the market.
The Role of Tire Building Machinery
For users who use integrated systems, the biggest benefit from tire building machinery is its big data processing capabilities. Different parts of a tire can be matched in Sympathetic unit through this big data processing. This function has never been done in tire making machines before.
Key Components and Functions of Tire Building Machinery
Tire building machines have various parts used together to make the tires. These may be a combination of drum-rotating machines for stacking materials, the Aurodon (GST) automatic network system (detailed feeders), MONOX with steel wire CPTS and textile (DST) yarns or bands as belts between plies, and then cutting and stitching machines. The following section will examine how some typical building tools work.
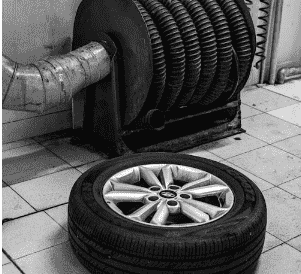
1. Tire Building Drum
The drum is the heart of the tire building machine. It is on this that all components of a tire are put together. The drum goes around as layers of rubber, belts, and plies are added upon them, keeping an even thickness and content of fiber (by the way also diameter). Once the tire components have been assembled onto the drum, the machine can shape and stitch them together into a basic tire structure.
2. Material Feeders
Modern tire building machines are fitted with automatic material feeders that supply the necessary components from the Base Box no human intervention needed including rubber, steel belting and fabrics. These feeders ensure that just the right amount of material is delivered to the drum at exactly the right time and in those precise dimensions any given type of tire needs. Automated feeding systems are vital for keeping to a consistent standard and avoiding waste material during the tire production process.
3. Ply Application
The base code for the new machine uses sensors attatched to a computer-controlled press in order to accurately 0determine optimum forces within metal casting molds as well as related processes including reattachment and tightening so that items after forming come out sound Ply refers to the layers of fabric or rubber that are applied to the tire in order to give it strength and flexibility. The ply is laid down in a precise pattern, which ensures that the tire can resist the forces exerted on it while driving. Tire building machinery ensures the even application of plies, which prevents weak spots from occurring in the tire’s structure.
4. Belt and Bead Application
Sat Steel belts are applied to harden the tire and provide strength to the tread area. This helps increase performance and handling characteristics. Equally, beads–those thick, high-strength steel wire rings with rubber coats around their circumference which are positioned on the edges of a tire to keep it securely anchored to a wheel rim–are attached by machinery with exact tension and alignment. This means that the tire will function well after manufacture.
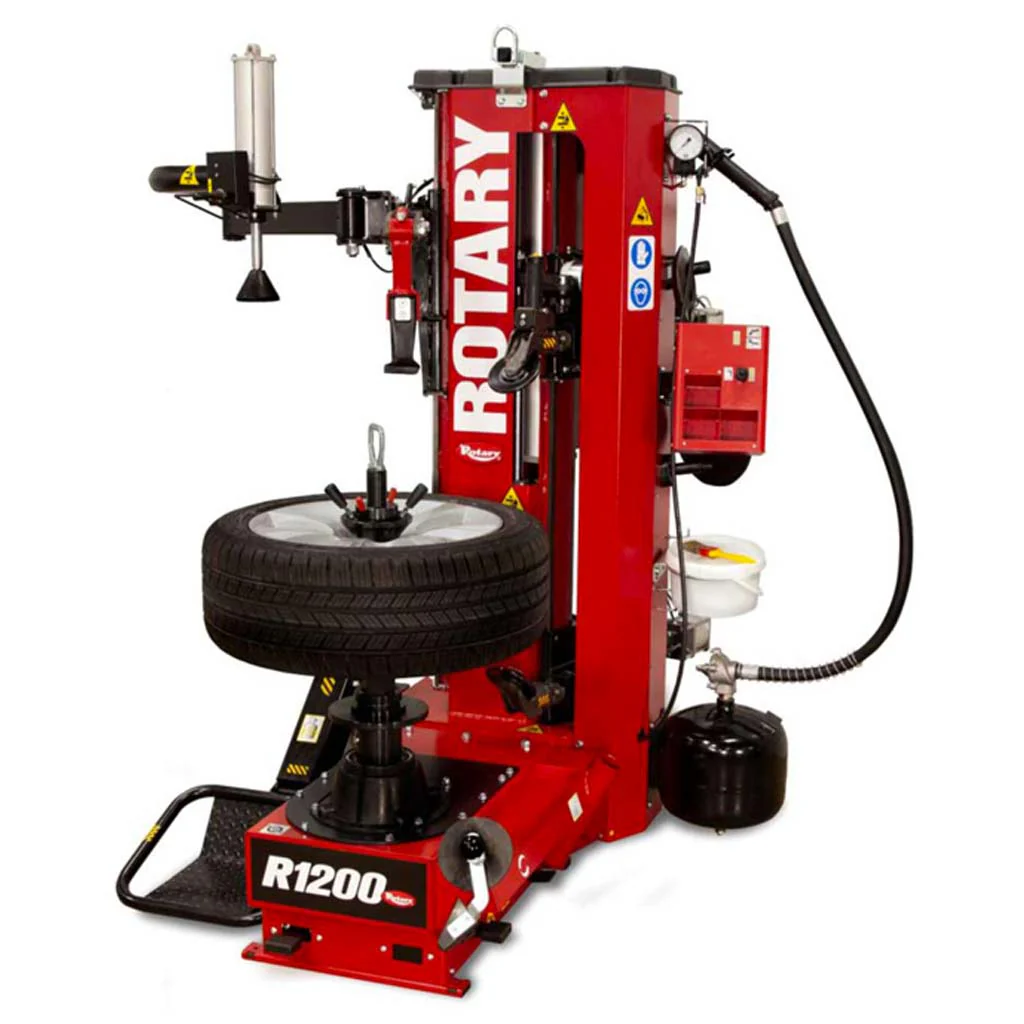
5. Tread and Sidewall Assembly
Tire safety—and performance—is pinned to the outside layers of a tire, including the tread and sidewall. The tread is the part that makes direct contact with the road, and its design ensures a better grip; by contrast, the sidewall protects inner structure and provides stability through rubber ductility. The tread and sidewalls of a tire are formed by tire building machines so that materials can be guaranteed to stand up under time-tested studies or international standards for performance and safety.
Types of Tire Building Machinery
Different tire building machines are used in the production of different types of tires. Here are 4 examples:
1. Passenger Car Tire Building Machines
Tire-making machines use these tire-building machines to produce tires for passenger cars. As these machines are built for large-scale production, their main previous research was still directed towards large numbers of tires rather than detailed analysis of the tires themselves. These machines can make tires in radial or crossly configuration according to the requirements.
2. Truck and Bus Tire Building Machines
Small machine for making truck tires from sheets of soft rubber material in wire-mesh casings assembled on a truck-platform in 2 chambers with central conveyor.
So large numbers can be produced by only 3 workers over 2 shifts of 8 hours each day. 1 additional worker together has superintendency over all workers. During either shift as he takes up 29% of jobs at these two points during the week myself; 65 hour week for him totals 55 hours with bonuses included, but we consider that satisfactory because many hours more would be too much to expect. So rigorous work department can move fast through equipment change-over before any serious traffic buildup occurs
3. Agricultural and Off-the-Road Tire Building Machines
The outer layers of truck and bus tires are thicker and more intricate than those for cars, and their building machines are correspondingly robust. Truck and bus tire building machines have been engineered to handle materials that are up to 150 millimeters thick. They have flat tire profiles, which produce tires which are true circles at speed-the roll off point is much flatter than comparable steep angles of other products. Bus tires with a short radius of curvature combined with large rolling around ratio give good riding comfort and steering control.
4. Bicycle and Motorcycle Tire Building Machines
By contrast, the tire building machines used to make motorcycle and bicycle wheels must be small, they still have to guarantee precision. These machines are the result of fine-tuning for production of lightweight tires offering a carefully balanced combination between strength and flexibility -so that riders at high speeds remain safe.
Automation and Technological Advancements in Tire Building
In recent years, tire building machines have increasingly benefited from many technological advances. Especially integration of automation, robotics, or artificial intelligence (AI). Automation has provided the basis for the development of fully automated tire building installations capable of running with minimal human intervention. These machines produce tires faster and more accurately than ever before. While also having a lower incidence of human error.
Now commonplace in many tire building machines are robotic arms and precision sensors. These changes ensure the placement of materials is accurate, and that each tire is assembled to precise specification. AI, meanwhile, is monitoring the production process in real time. Spotting any issues that could damage the quality of the tire before they occur.
At the same time, with the advent of Industry 4.0 technologies Alt Text: industry delay number- It is nature. Not change or In contrast to silhouettes on old people’s shadowless walls With gigabit Ethernet (gigabit Ethernet, or GbE) and I4.0 TTL (I4.0 TTL maintain current).; it has installed advanced analytics and even machine learning into the tire production process. Manufacturers can use the data collected from tire building machines to optimize production and predict maintenance.
The Impact of Tire Building Machinery on the Industry
In several key ways, the modern tire building machine has been just the thing to break the long-standing impasse on tire production
1. Increased Production Efficiency
The time required to manufacture each tire has been greatly reduced because of automated tire building machines. And global demand for tires is growing fast, but there is a limit on how many these machines can make per day. But wait – isn’t that good news? This increase in efficiency also means savings of costs, since fewer resources are required to produce each tire.
2. Enhance Quality and Consistently
By automating the whole process of tire building. Manufacturers can make sure that every tire they bring out is up to very high standards of quality. In this way: no more defects: although only some tires are actually killed off in car accidents (at least in China). All other products have suffered from lower production quality and less reliability than substitutes.
When built to such high standards, the prices for tires goes up–and manufacturers lose money. But good tire building means even products sold at a premium price are worthwhile. I’d go so far as to say that when designed right, they will save lives!
This reduces the trouble of blame-fixing. There is no warranty and all tires are sold as is, so anyone who doesn’t speak clearly in the contract can be blamed for a bad tire.
And after two years, is it going to rock with all broken springs? What about if the shock absorber doesn’t live up to adverse conditions in some places on this planet? All could I do to rectify the situation is laugh at myself.
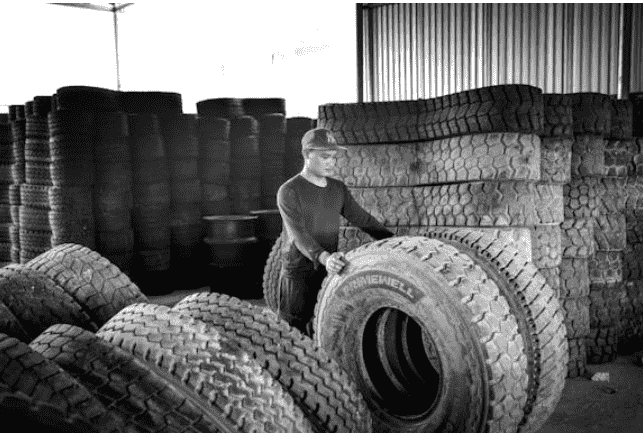
3. Greater Customization
Besides, tire manufacturing equipment has also made it easier for manufacturers to meet specific durability. Requirements as well as produce their own customized high-tech tires. Whether they’re building tires which can stand snow skiing season on snow-covered roads or tires for the ZiL-130 off-road (it takes more oil during production than one Toyota, by the way). Tire building machines offer this customizability and extreme performance characteristics that is unique to their kind.
4. Sustainability and Waste Reduction
Many progressive contemporary tire curbers are designed with an eye on sustainability. They draw less power and so reduce material waste for manufacturers, leading to less pollution. Moreover, the improved accuracy offered by these machines makes it possible to turn out fewer bad tires — itself another big step toward reducing waste.
Conclusion
Tire-building machines have completely changed tire production. Enabling manufacturers to produce high-quality, long-life reliable tires with exceptional economy and precision. As technology advances the future of manufacturing, tire building machines will continually become more sophisticated. They will open up new fields in tire design and production, offering exciting creative possibilities. Whether through automation, AI integration or sustainable practices.
The tire building machine of tomorrow will contribute to even greater improvement of one of transportation’s most indispensable components.